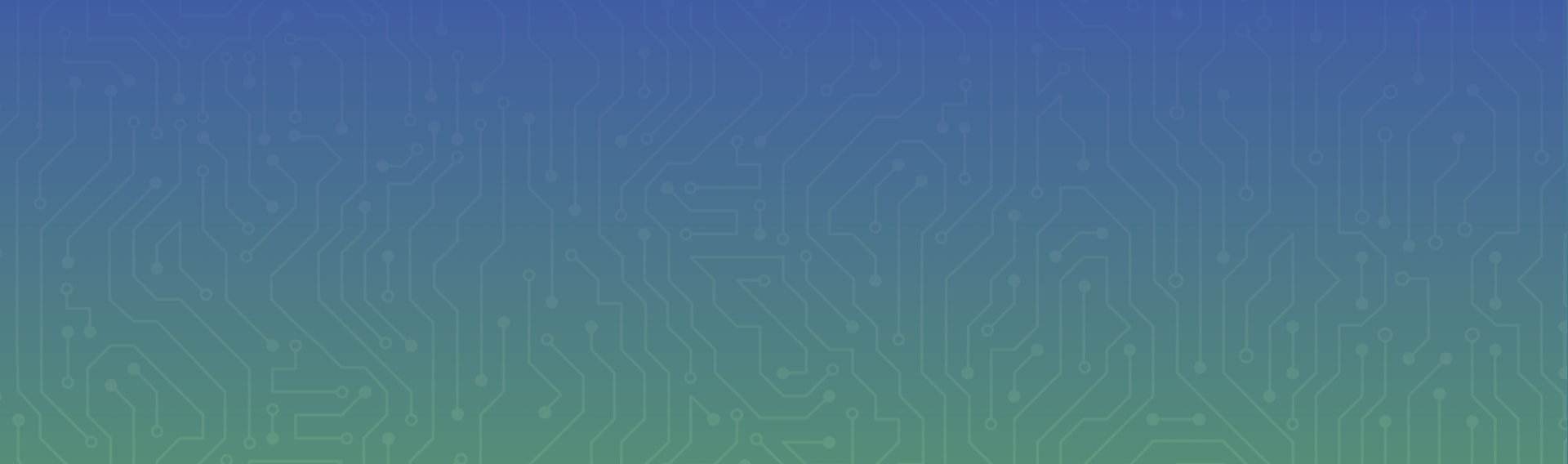
Inventory Control analyst- Memphis, TN
- On-site
- Memphis, Tennessee, United States
- Supply Chain: Purchasing & Planning
Seeking a Inventory Control analyst at our new Memphis facility to assist our Supply Chain department in controlling inventory and cost associates with our business.
Job description
Position Summary:
The Inventory Control Analyst will prioritize, assign, and lead activities associated with recording, tracking, and control of all inventory items within the distribution environment. In this role, you will oversee cycle counting, review inventory slotting requirements, handle inventory inquiries from internal customers and establish new part/bin setups within the facility. This position requires knowledge of inventory concepts and practices, and the ability to review inventory discrepancies, conduct trend or root cause analysis and lead a work team. This position will report into a Program Manager/Director level.
Responsibilities/Duties:
Oversees inventory control activities within the distribution environment. Prioritizes and assigns work, trains employees, and monitors the progress of tasks through to completion.
Distributes work among team members, rebalancing as necessary to allow for special projects and incoming requests.
Supervises cycle counts of inventoried items; ensures daily counts are loaded and adjusts shift times as needed for completion.
Coordinates the process of researching, identifying, and adjusting discrepant product counts within multiple product lines.
Research adjustments to ensure due process was followed.
Performs inventory checks in response to both internal and external customer email requests.
Research systematic and physical inventory movement to identify discrepancies and responds by making inventory adjustments, part conversions, systematic transactions, or by initiating special projects.
Compiles data from cycle counts and inputs into ERP/WMS system for adjustment approval and finalization.
Investigates and reports root cause analyses of system discrepancies and transaction errors; adjusts inventory and recommends process improvements to resolve identified problems.
Communicates and interacts with other departments, supervisors, planners, buyers, managers, and customers to adjust discrepant inventory, locate lost inventory, complete parts rolls, and resolve discrepancies.
Tracks and monitors part demand activity for warehouse slotting requirements.
Coordinates the systematic part conversion process, the consolidation and return of wrong parts pulled, and the assignment of primary and overflow pick bin locations for all newly received parts numbers.
Coordinates items slated for both physical and systematic disposition.
Prepares documents and produces reports, spreadsheets, charts, and training documentation.
Performs other duties and special projects as assigned.
Qualifications
Education and Experience:
Bachelor’s degree preferred, equivalent experience.
4-7 years of related experience in inventory control or warehousing
Job requirements
Responsibilities/Duties:
Oversees inventory control activities within the distribution environment. Prioritizes and assigns work, trains employees, and monitors the progress of tasks through to completion.
Distributes work among team members, rebalancing as necessary to allow for special projects and incoming requests.
Supervises cycle counts of inventoried items; ensures daily counts are loaded and adjusts shift times as needed for completion.
Coordinates the process of researching, identifying, and adjusting discrepant product counts within multiple product lines.
Research adjustments to ensure due process was followed.
Performs inventory checks in response to both internal and external customer email requests.
Research systematic and physical inventory movement to identify discrepancies and responds by making inventory adjustments, part conversions, systematic transactions, or by initiating special projects.
Compiles data from cycle counts and inputs into ERP/WMS system for adjustment approval and finalization.
Investigates and reports root cause analyses of system discrepancies and transaction errors; adjusts inventory and recommends process improvements to resolve identified problems.
Communicates and interacts with other departments, supervisors, planners, buyers, managers, and customers to adjust discrepant inventory, locate lost inventory, complete parts rolls, and resolve discrepancies.
Tracks and monitors part demand activity for warehouse slotting requirements.
Coordinates the systematic part conversion process, the consolidation and return of wrong parts pulled, and the assignment of primary and overflow pick bin locations for all newly received parts numbers.
Coordinates items slated for both physical and systematic disposition.
Prepares documents and produces reports, spreadsheets, charts, and training documentation.
Performs other duties and special projects as assigned.
Qualifications
Education and Experience:
Bachelor’s degree preferred, equivalent experience.
4-7 years of related experience in inventory control or warehousing
or
All done!
Your application has been successfully submitted!